How Continuous Casting Furnaces Work?
Ever wondered how much work goes into making metal rods and bars? The innovative Continuous Casting Furnace is going to amaze you.

Ever wondered how much work goes into making metal rods and bars? The innovative Continuous Casting Furnace is going to amaze you.
This innovative machine eliminates the need for conventional method of pouring molten metal into individual molds and waiting for them to solidify, as it maintains a continuous stream of metal.
Continuous Casting Furnaces are commonly known for their use in the production of metals such as steel and aluminum.
However, these versatile furnaces can also be adapted for gold production. To better understand how Continuous Casting Furnaces work for gold, let's take a closer look at the process:
1. Melting Gold:
The first step involves melting raw gold down until it becomes a liquid.
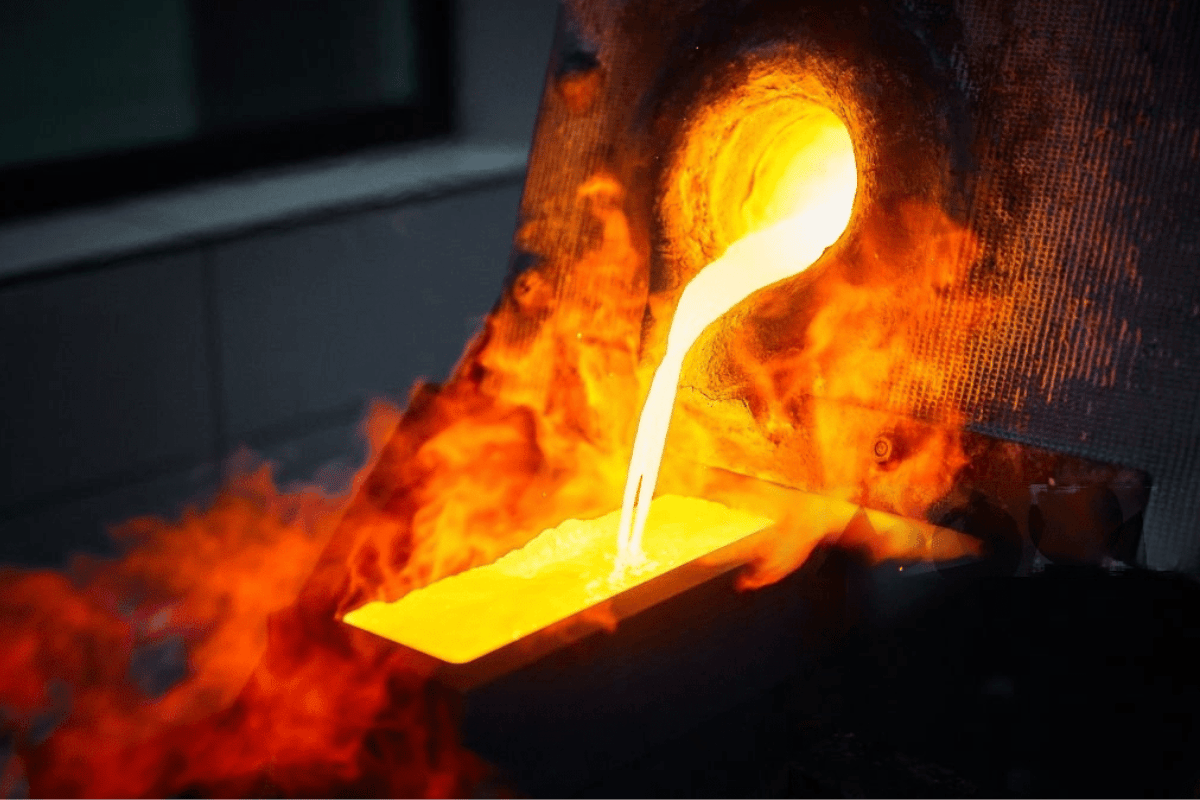
This is achieved by placing the gold in a high-temperature furnace, where it is heated until it reaches its melting point and transforms into a molten state.
2. Continuous Casting:
Once the gold is molten, it is poured into a specialized mold within the Continuous Casting Furnace.
Unlike traditional casting methods, which use individual molds for each piece, the Continuous Casting Furnace employs a continuous casting system.
The mold is designed to be continuously cooled with water, allowing the molten gold to solidify rapidly.
This results in a seamless production process with consistent and precise results.
3.Solidification:
Watch as the stream of molten gold pours effortlessly into the chilled mold, instantly transforming into a solid state.
This ingenious continuous casting technique ensures an uninterrupted flow of production, eliminating the tedious process of using single molds and minimizing the intervals for each casting cycle.
4.Cutting & finishing:
After the gold has turned into a seamless strand, it is precisely sliced into specific lengths using specialized cutting machinery. These lengths are tailored according to the intended purpose of the gold, whether it is meant for adorning jewelry, creating investment bars, or fulfilling other purposes.
Following cutting, the gold may also undergo additional refinement techniques like polishing to achieve the desired appearance and level of perfection.
5.Quality Control:
In order to maintain the high standards expected, every step of the production process is accompanied by rigorous quality control measures.
These controls encompass evaluating samples of the cast gold to ensure purity and conducting thorough visual inspections to identify any flaws or abnormalities.
Ultimately, our commitment to maintaining the integrity and consistency of our gold is unwavering.
Conclusion
To summarize, the process of utilizing Continuous Casting Furnaces for gold includes melting raw gold into a liquid state, which is then steadily poured into a water-cooled mold to form a continuous strand.
Check Out: Continuous Casting Furnaces
This streamlined procedure boasts numerous benefits such as heightened efficiency, increased uniformity, and better quality control, making it a highly sought-after technique for gold production in a diverse range of industries.
Leave a comment